Project Story 01
大手ビールメーカーの
工場立ち上げに挑め
ソリューション開発・提案
Project Outline
TLVでは既存の蒸気設備・システムにおける診断や課題解決だけではなく、プラントの新設時から立ち上げに関わるケースも少なくない。その代表事例であり、TLVにとってエポックメイキングな挑戦となったのが2000年に竣工した大手ビールメーカーの工場の新設プロジェクトだ。「蒸気周りの設備・システムのみならずプラント全体の立ち上げをプロジェクトマネージャーとして担当し、イニシャルコストおよびランニングコストの削減を実現する」。TLVにおいて前例のないミッションに挑むことになったのが、当時28歳・入社6年目にしてCE部門における東日本の責任者を担っていた藤川である。
Project Manager
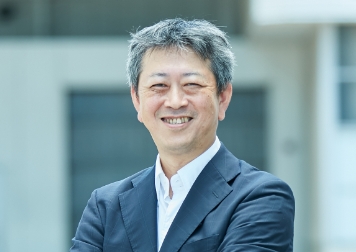
藤川 雄一
Solution Sales本部 本部長
1994年入社
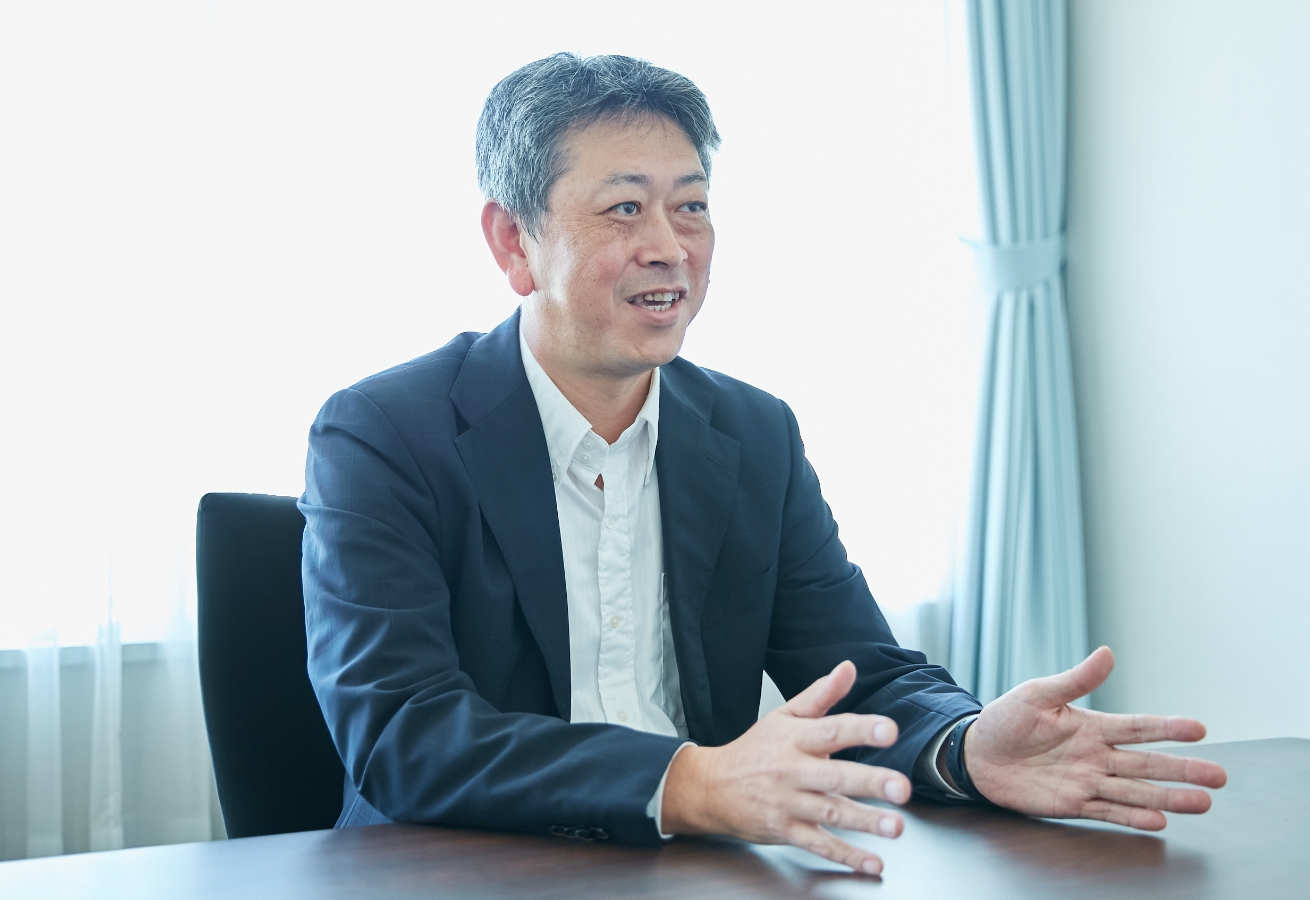
Scene 01 / Order
蒸気周りだけでなく
プラント全体を見て欲しい
国内大手ビール会社における新工場建設プロジェクトが動き始めたのは1997年のこと。技術職としてTLVに入社した私は当時、コンサルティングエンジニア(CE)を担当。入社6年目にしてCE部門における東日本の責任者を任されていました。私が本案件を担当することになったのは、同じエリアで営業組織を束ねる責任者からの相談がきっかけです。私にとって新工場の立ち上げに携わるのは2回目で、入社4年目にも一度携わったことがありました。とは言え、前回は蒸気設備に関連する部分のみ。プラント全体の設計から手掛けるのは初めてのことでした。
お客様からのオーダーは、プラントの立ち上げにかかるイニシャルコストと日々の稼働にかかるランニングコストを抑えること。ビールの製造には熱源となる蒸気が欠かせず、プラントの核となる蒸気システムのスペシャリストであるTLVに相談が持ちかけられたのでした。
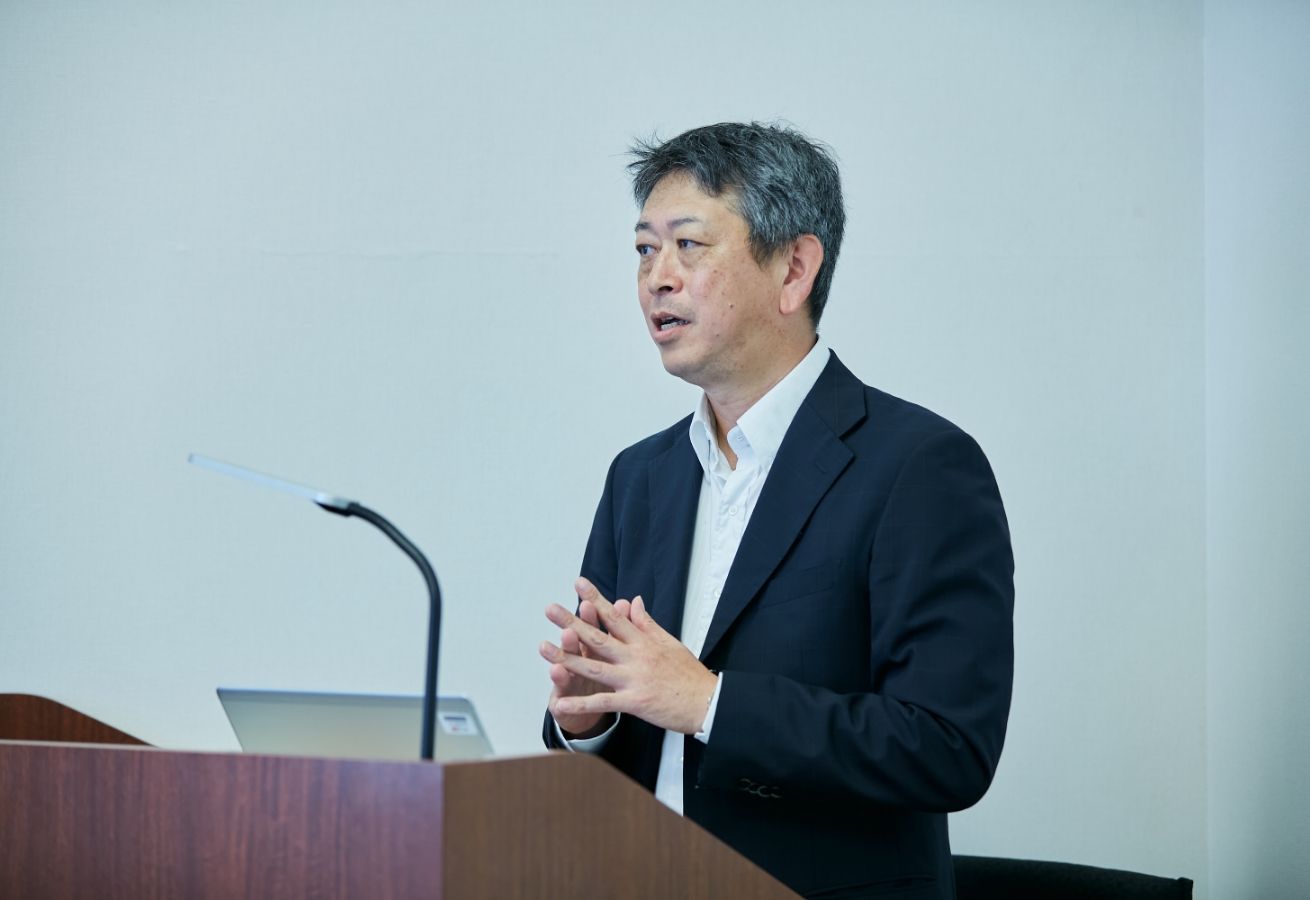
Scene 02 / Action
既存工場の課題から
新工場のプランを設計
お客様とは以前からお付き合いがあり、スチームトラップの診断器(TrapMan)の販売や、それを活用した診断サービスの提供、ドレン・廃熱回収システムの導入などで省エネルギー活動のサポートをしてきていました。そのため、蒸気システム周りの知見はありますが、プラント全体については未知のことばかり。まずはビールの生産プロセスを学ぶことからはじめ、加えて既存工場における課題を探りソリューションを導き出すことにしました。
お客様であるビール会社は全国に工場を展開されています。その中の最新の工場を、私たちはベンチマークの対象に設定しました。私ともう一名のメンバーで徹底的な診断を行ったところ、多くの無理や無駄があることがわかりました。私たちはそれらの課題とソリューションに加え、それによって実現できる具体的な削減コストを資料化。お客様に提案したところ、「それだけコストダウンできる可能性があるなら一緒にやりましょう!」と心強いお言葉をいただけました。
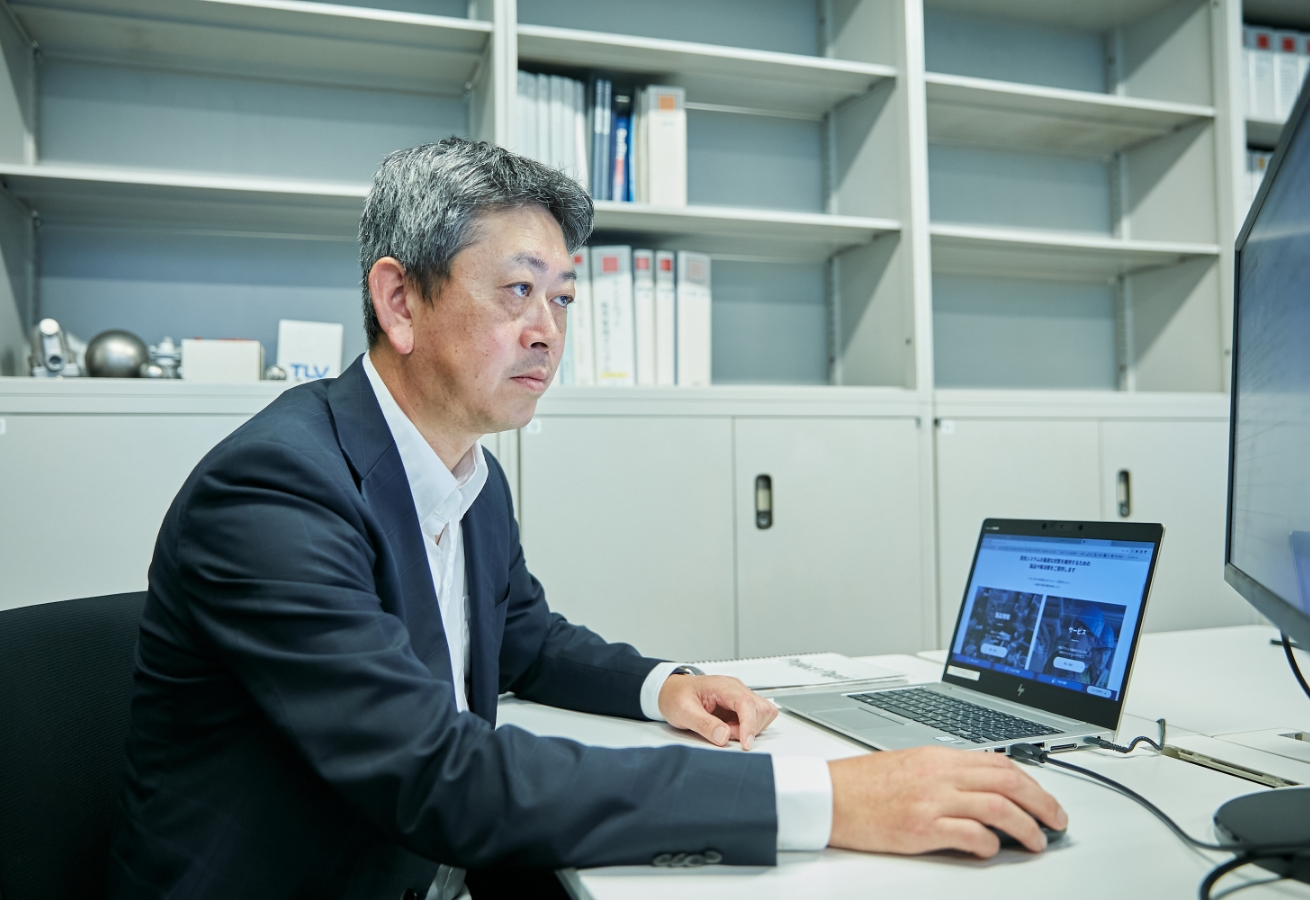
Scene 03 / Solution
ボイラの小型化や
配管の小径化等に着手
新工場の建設にあたり、私たちはお客様とコンサル契約を締結。お客様と同じ立ち位置で、プロジェクトマネージャーとして建設会社や施工会社、装置メーカーらの指揮を執ることとなりました。プラント全体のパフォーマンスを最大化した上でコストダウンを目指す中で、私たちは8つのテーマを設定。既存工場の診断を通じて得た課題をもとに、無理や無駄の解決に取り組んでいきました。
例えば、ボイラの変更もそのひとつです。既存工場で使用されていた大型の水管ボイラは高圧で大容量の蒸気を作り出せますが、低稼働時には大きなロスが発生します。この問題を、私たちは小型貫流ボイラをたくさん設置することで解消。必要な量だけ蒸気を作り出せる仕組みにすることで高効率かつ省エネを実現していきました。
また、蒸気配管のサイズ変更も実施。既存工場で採用されている配管は必要以上に径が大きく、ゆとりの分だけ放熱ロスが発生していました。そこで私たちは適正なサイズに変更。3サイズほど小さくすることでロスを解消し、同時にイニシャルコストも削減しました。他にも、煮沸釜とボイラの位置を隣に設けることで放熱ロスを減らすなど、さまざまなソリューションを形にしていきました。
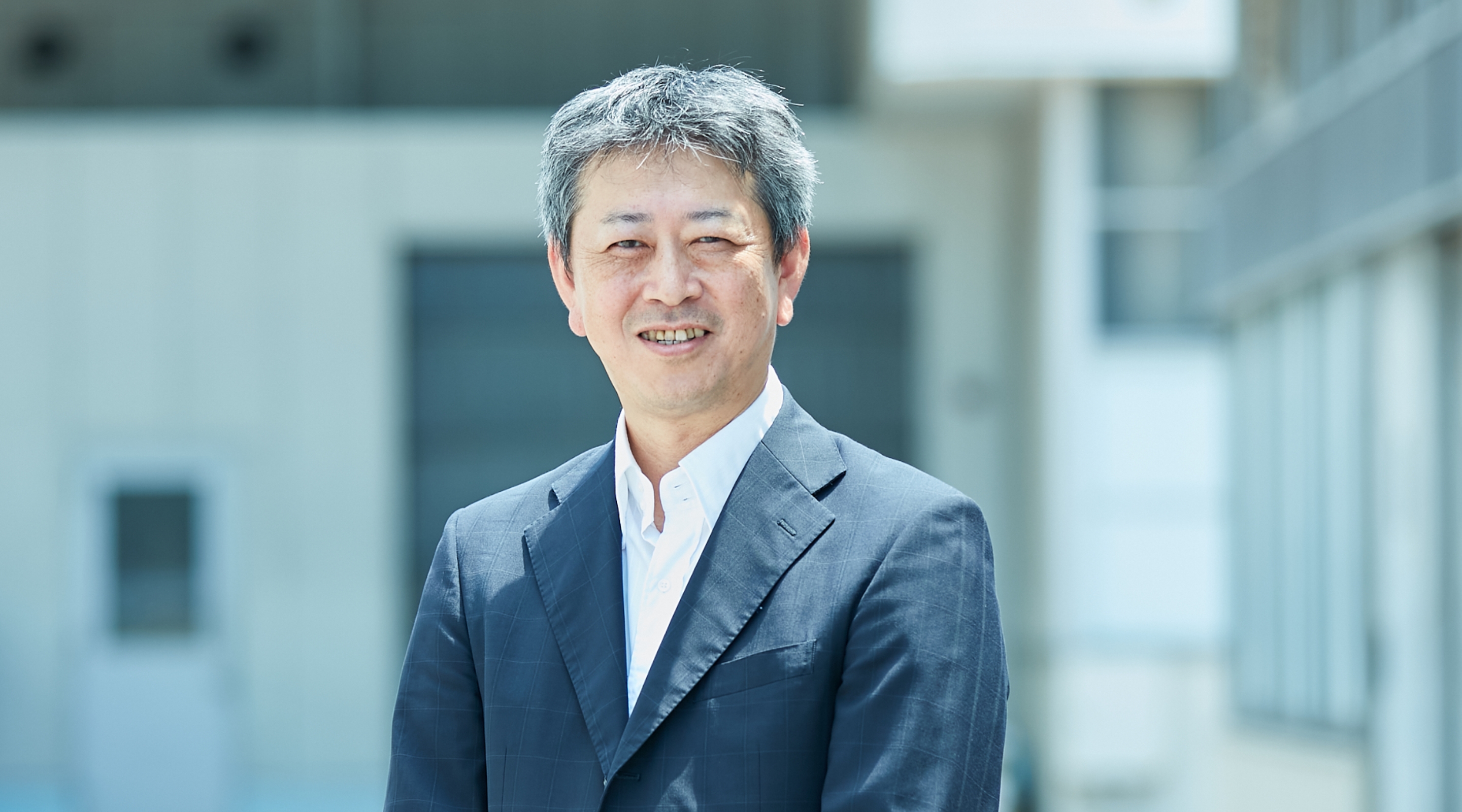
Scene 04 / Result
大幅なコストダウンと
環境負荷の低減を実現
プロジェクトに要した期間は、およそ3年。初めてのチャレンジですから、その間は苦労の連続。プロジェクトマネージャーとして各分野のプロと対等に議論するため、あらゆる時間を費やして勉強に励むなど努力を重ねました。ようやく完成にこぎ着けたときも、最初の1週間は工場に滞在。配管サイズを小さくした箇所に、本当に蒸気が流れるのか。さまざまな不安がありましたが、大きなトラブルもなく無事に竣工を迎えることができました。
結果、蒸気関連機器(配管・装置、弁・計器類など)にかかるイニシャルコストを30%削減。ランニングコストに関しては、同生産能力を持つ既存工場の燃料原単位(重油L/KL)で比較すると約25~40%削減(季節変動あり)に成功するなど、提案時よりも大きな成果を実現することができました。また、ボイラ燃料をLPGにすることで、嫌気性廃水処理設備においてメタンガスの回収、水力・風力・太陽光発電導入、再資源化率100%を実現。地球に優しいリサイクル工場のビール工場の建設に貢献することができました。お客様からも大きな評価をいただき、最近では海外工場の省エネ対策のご相談を頂くなど、そのご縁は今も続いています。