iBPSSM.net
Innovation of steam-using
equipment management
through wireless monitoring
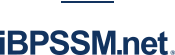
Maintaining steam-using equipment
in its optimal state
Day by day, steam plants gradually deteriorate. To support the safe and reliable operation
of production facilities and promote energy conservation, TLV offers cutting-edge steam system management solutions powered by wireless monitoring sensors. This innovative service
helps prevent costly, unexpected plant shutdowns while dramatically reducing steam waste
—improving energy efficiency and lowering CO2 emissions.
Recognized for its significant contribution to sustainability, TLV was awarded the 2021 Energy
Conservation Grand Prize – Minister of Economy, Trade and Industry Award (Business Model Category).
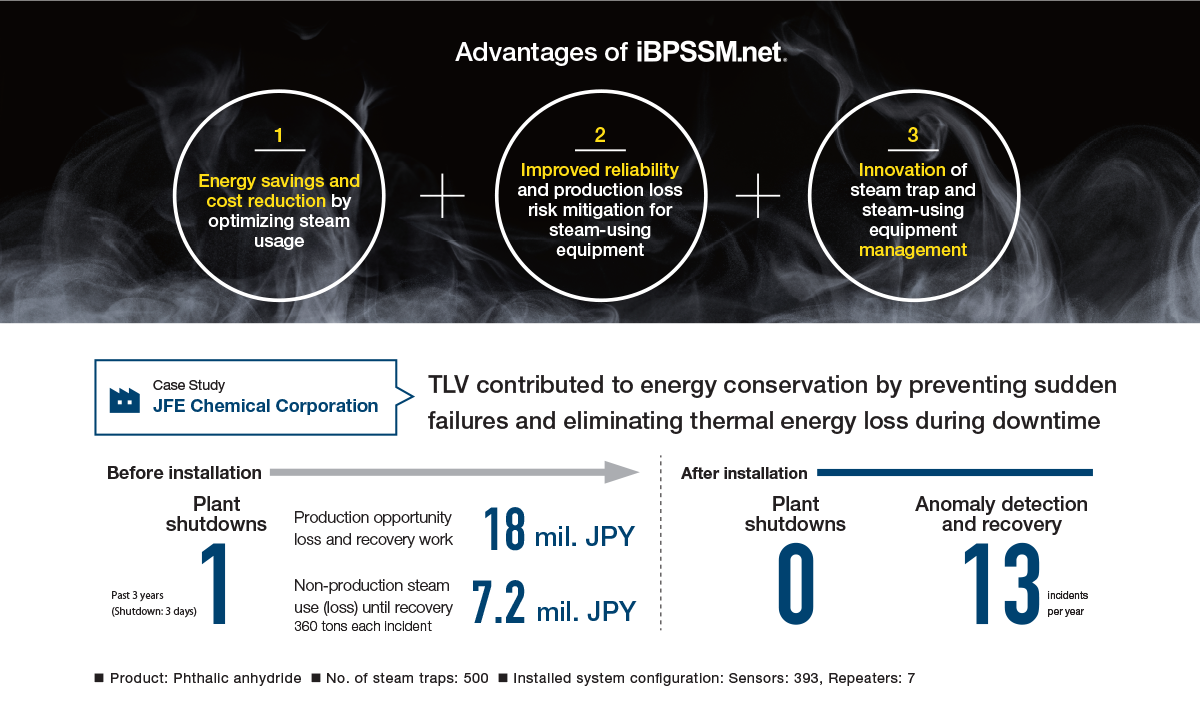
Our consultants assist customers in supervisory operations
Our process starts with listening to our customers' concerns. Consulting engineers then visit the site to assess the situation firsthand, providing expert guidance and maintenance support to optimize safety and energy efficiency.
Wireless monitoring to visualize and contribute to planned maintenance
Continuous monitoring with wireless sensors identifies steam trap failure trends, enabling proactive maintenance of steam control equipment and ancillary systems before issues arise.
Identify the root cause of repeated failure through inspection and data analysis
When a specific steam trap repeatedly fails, accumulated data and on-site inspections help identify patterns and pinpoint the root cause, enabling targeted improvements and preventive measures.

Step | Services provided | Examples | ||
---|---|---|---|---|
1 Understanding the Issues |
On-site equipment inspection. Formulate improvement measures for management operations. |
|
||
2 Scope Definition |
Evaluate the importance of steam-using equipment. Select steam traps to monitor. |
|
||
3 Monitoring Specifications |
Determine optimal sensor locations, monitoring cycles, etc. |
|
||
4 Installation |
Building the monitoring system. Installation of surface temperature/ultrasound sensors. | |||
5 Operational Support |
Operational support for monitoring results. Establish operation actions from detected failures. |
|
||
6 Verification of Results |
Continuous support for stable and safe operation of steam-using equipment and promotion of energy conservation |
|